The annual Sustainability Leadership Award honors an employee who embodies the firm’s commitment to a clean, safe and healthy environment while developing innovative and sustainable solutions for projects and clients. This year’s award was presented to Diana Chumak, P.E., an engineer in the firm’s Water + Environment market, for her innovative approach to water reuse evaluation at electric vehicle (EV) battery manufacturing facilities. Diana developed a methodology for identifying sources of wastewater within the production process that can be reclaimed and treated for reuse within the facility, thereby reducing the burden on local municipal water systems. The approach also quantifies reuse options on the basis of direct and indirect costs. We recently sat down with Diana to learn more about the sustainable solutions found through her successful study.
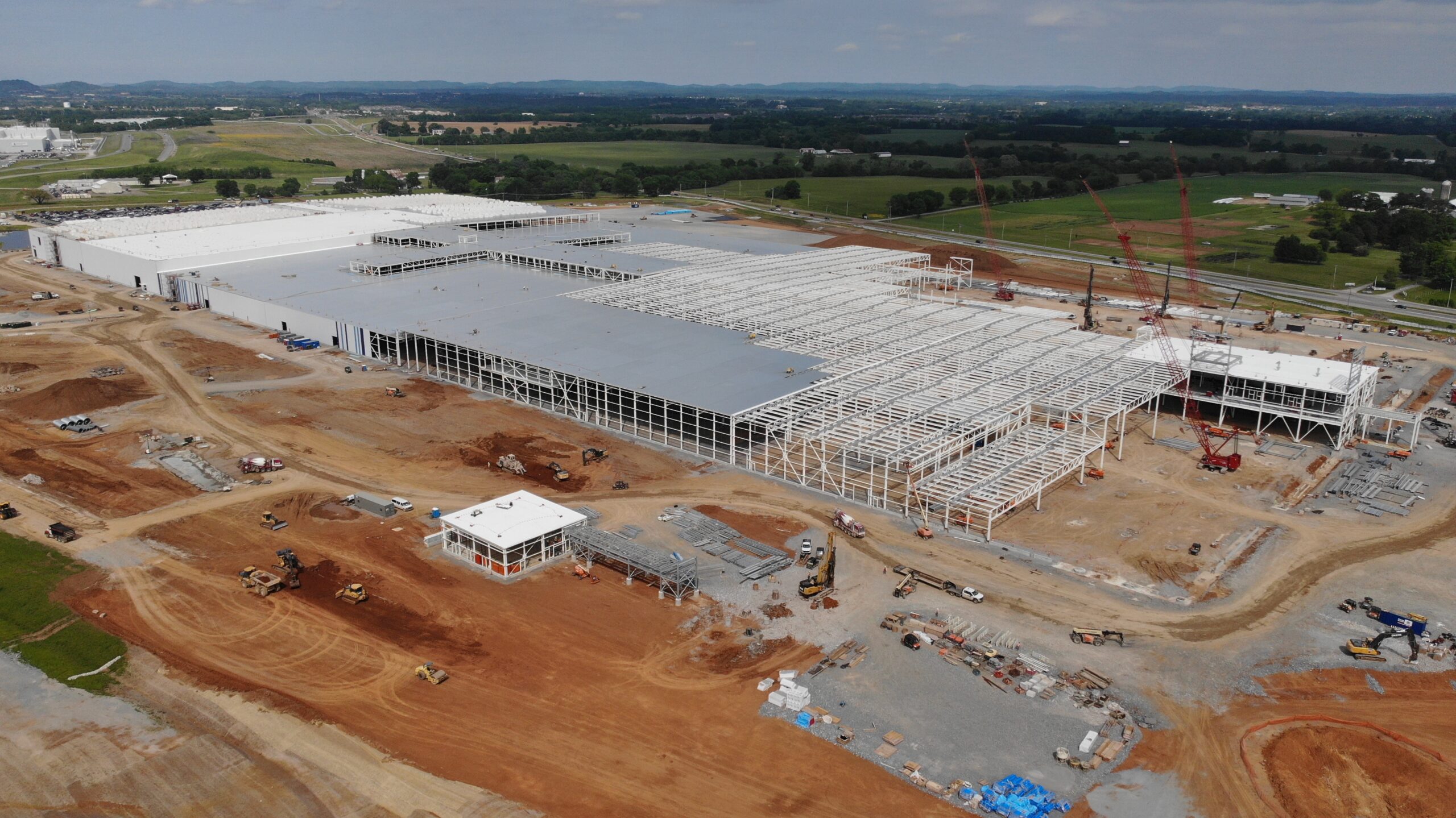
What was the need or reason behind this study?
Diana Chumak: EV battery manufacturing facilities are the new, hot thing with their demand being driven by the current consumer market for EVs, government incentives for electrification, and a need driven by environmental and sustainability considerations. They’re being built everywhere, but especially in small communities where a large new facility can have a disproportionate water demand compared to the per–capita demand of the communities they are built in. For this particular project, our client wanted to determine the feasibility of implementing a water reuse process to offset their high water demands. Typically, a large volume of relatively high-quality wastewater from the battery production process is discharged to a wastewater treatment plant, but with this study, we posed a new question—what if we captured that water and reused it instead? Aware of my interest in sustainability practices, Randy Booker, who’s a Senior Vice President and the Technical Practice Leader in our Water + Environment market, enlisted me to develop a study establishing an innovative approach to evaluating water reuse at these production facilities.
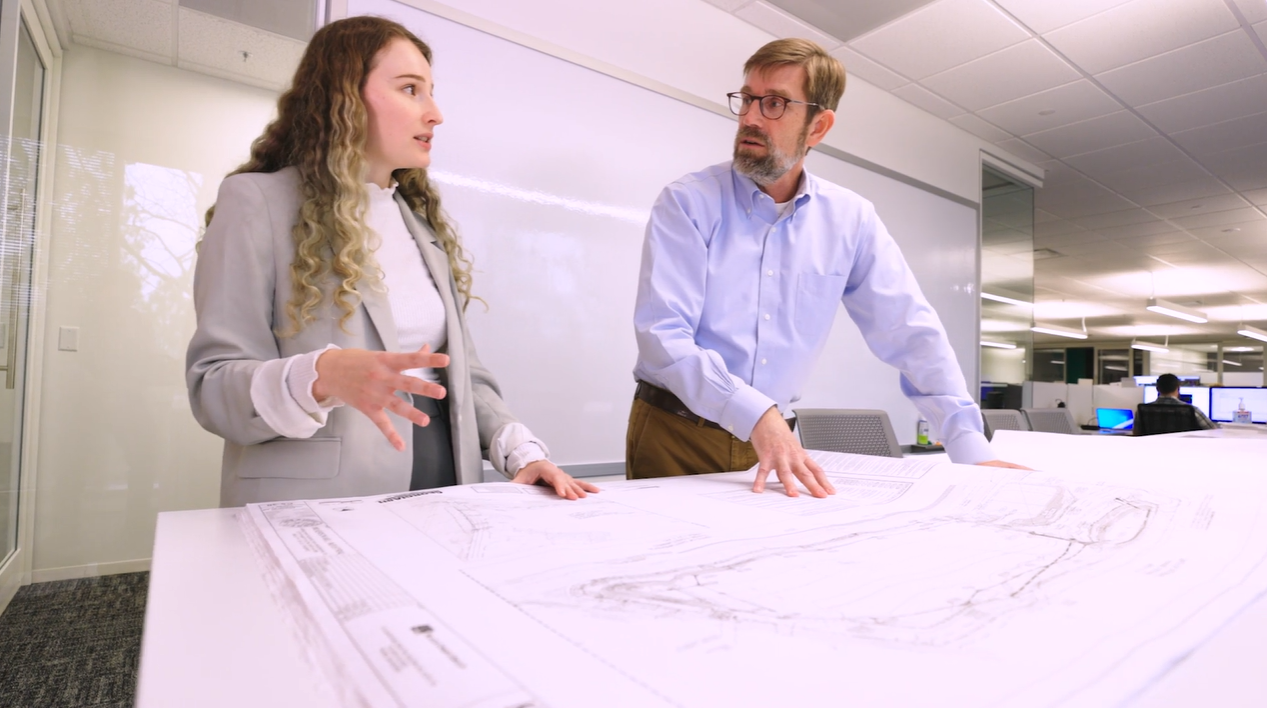
What are the benefits of water reuse in a manufacturing facility?
Diana: By implementing reuse in a battery production facility, there’s a domino effect of benefits, meaning we reduce the volume of water we consume and the volume of wastewater we discharge. These reductions save costs, lower the energy consumption related to distribution, and improve the resiliency of the facility all while reducing strain on local utilities. The most impactful benefit, however, is seen in replacing the water from the utility with a high-quality reuse source. With this, the operational efficiency of the facility is significantly improved, which reduces the overall volume of water needed in the first place. The individual reuse scenarios we developed each have their own particular benefits as well.
Since few resources existed, describe how you developed the tools and methodology to conduct the evaluation.
Diana: There was no textbook or template that could be used as an instructional manual. Instead, the study had to be a highly customized, analytical and quantitative effort.
The methodology we developed tells us how much operational and embodied carbon is released from implementing our various water reuse options versus the carbon released from traditional water supply and wastewater disposal of the same volume. We compiled comprehensive material inventories, which allowed us to quantify and compare which scenario had higher net emissions. Recognizing that consideration of water reuse options should be subject to a holistic impact assessment, we developed a methodology that quantified reuse options based on both direct costs (capital, O&M and life cycle financial payback) and indirect costs. Indirect costs mainly consisted of the carbon footprint—made up of embodied carbon plus operational carbon—of implementing the possible reuse options.
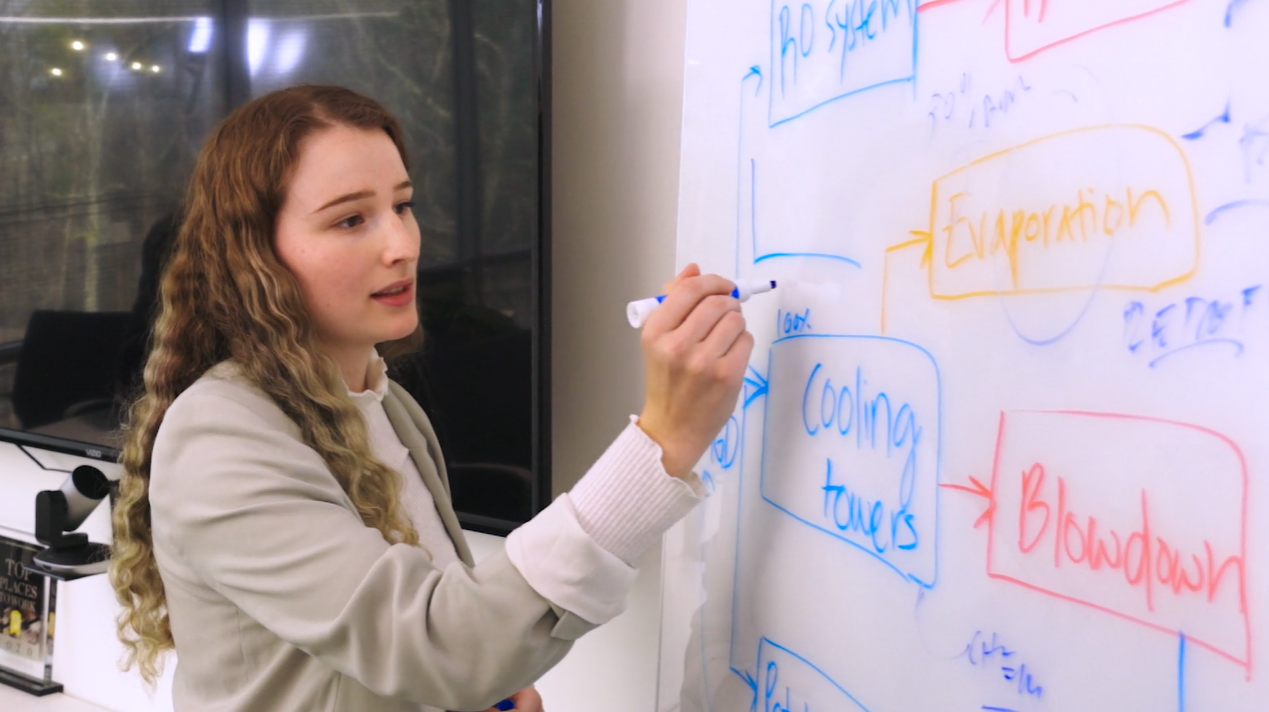
How can this work be applied to other projects?
Diana: While calculating direct costs is a pretty common practice, incorporating indirect costs isn’t yet, so indirect impacts are largely left out of the decision-making process currently. We can apply this methodology of calculating those indirect costs, not only to other battery production facilities, but other projects for clients who are interested in determining what those indirect costs are and helping them reach their sustainability goals.
Which water reuse scenario did you recommend and why?
Diana: Options for reuse included cooling tower blowdown, reverse osmosis concentrate, HVAC condensate, cooling tower evaporative plumes and rooftop stormwater collection. Our most feasible reuse scenario ended up being a rooftop stormwater capture system with an underground tank for storage. This option resulted in the shortest payback period and actually resulted in net neutral emission when compared to the same volume of water being purchased from a local utility.
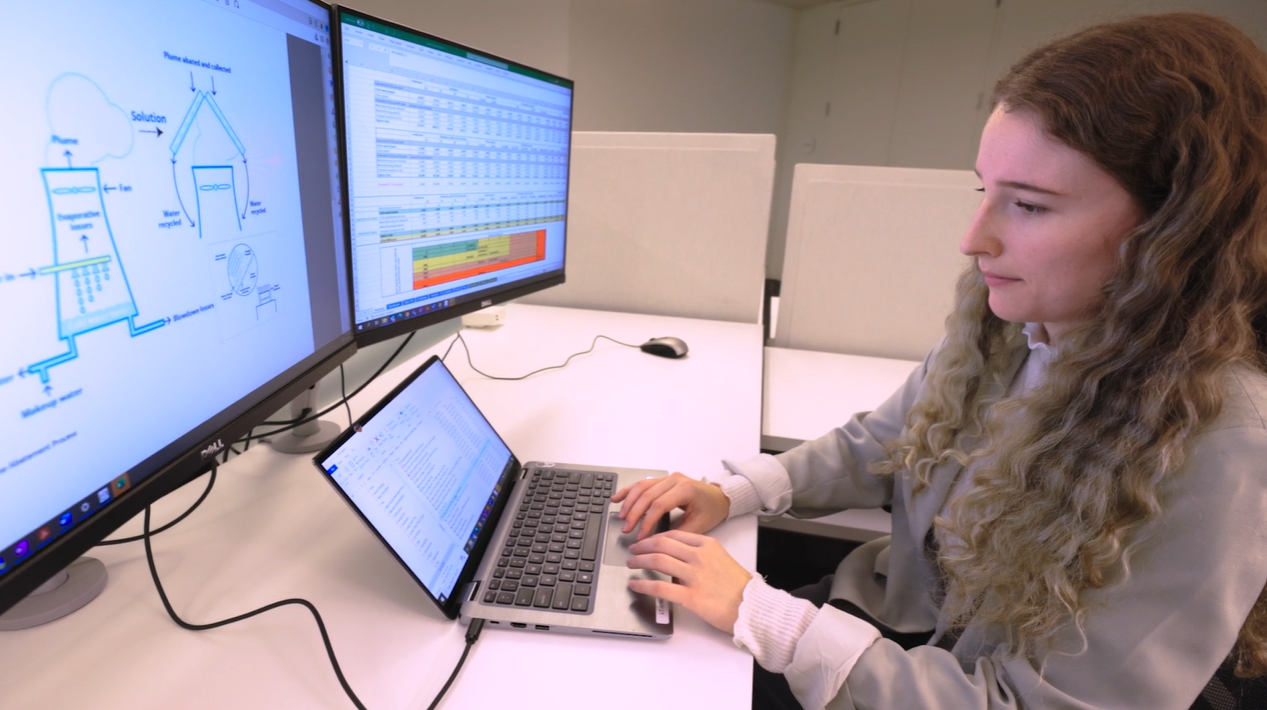
How have your findings been received by the client?
Diana: Our client was really pleased to receive the results of our study. They were excited to take our methodology and our findings and implement them in their future facilities that were in the initial phases of planning and design.
How do you think this work will impact the industry moving forward?
Diana: I think this study and its findings could change the way that this client—and ultimately other EV battery manufacturers—prioritize water reuse as opposed to considering it as an afterthought.
I ascribe to the idea that one person can make a difference and that we should be proactive instead of reactive. As someone passionate about sustainability, I believe that, instead of just solving environmental problems, we should be creating sustainable options. This project allowed me to test myself and pursue a passion within my profession.