The site itself, positioned partially in a flood plain, left little room to build outward, spurring the Gresham Smith team to more creative solutions that used existing tankage where possible, and that increased function without extensive building. To expand treatment capacity within limited space, Gresham Smith’s plan called for a 15-mgd sequencing batch reactor to replace the plant’s 10.6-mgd aerated bio-tower facility. The new facility is the largest sequential batch reactor in the United States and will provide more efficient processing for higher volumes. It achieves current standards for effluent nutrient levels, and can easily be re-fitted with micro or ultra-filter membrane technology should future standards become even more stringent.
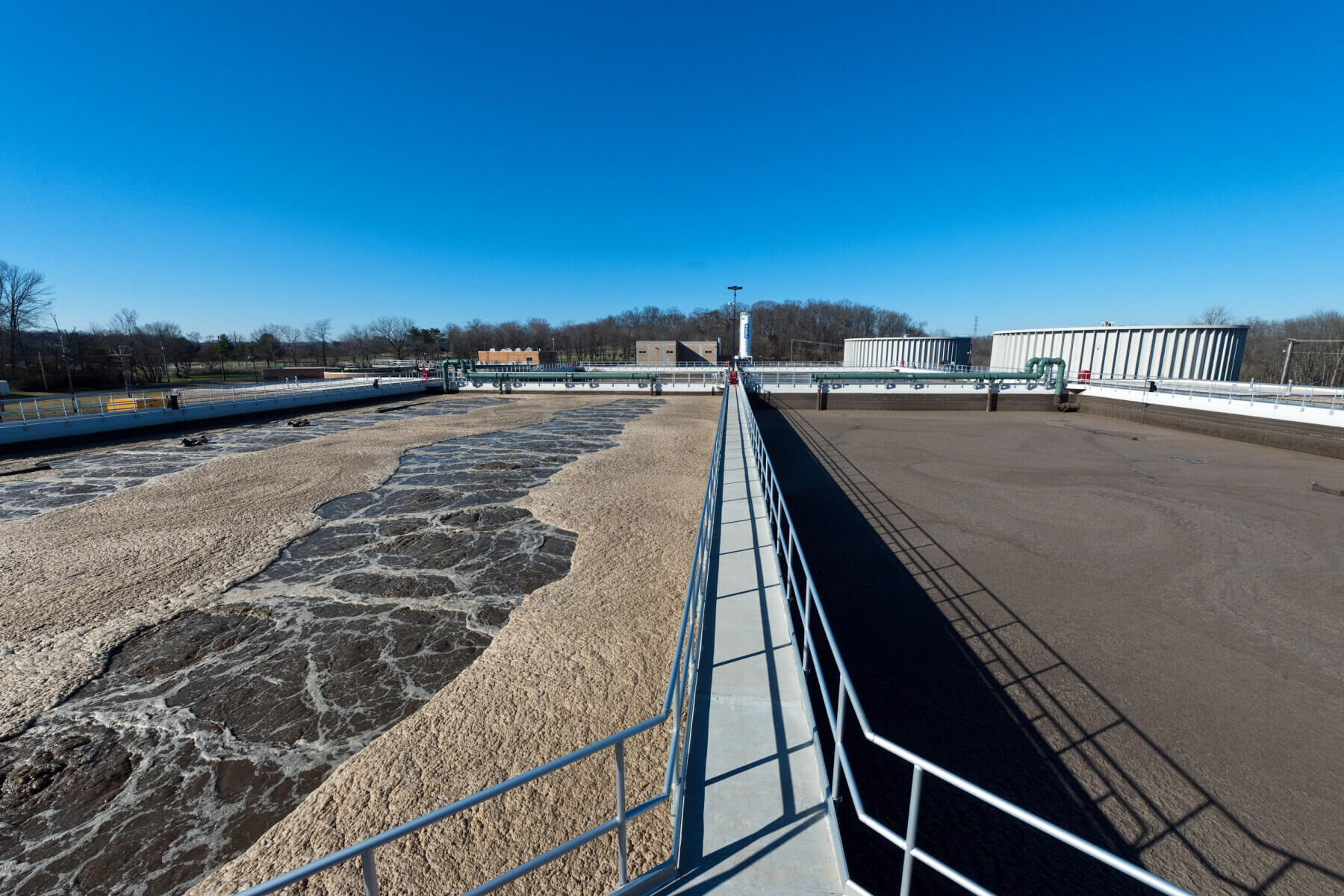
The expanded plant also incorporates an indirect thermal dryer that converts biosolids into 12.5 dry tons per day of a sustainable Class A product that can then be used as an agricultural soil supplement. The project includes a Therma-Flite IC 10000 dryer, the first used for municipal biosolids, which can process 10,000 lbs. of water per hour. It was installed in response to BGMU’s concerns about their existing method, which involved dewatering biosolids in a single centrifuge and hauling the waste 40 miles to a landfill for final disposal. The thermal dryer represents an environmental and economic improvement over this previous practice, as it promotes sustainable use of waste and is projected to reduce BGMU’s residuals management costs by at least 30 percent per dry ton.
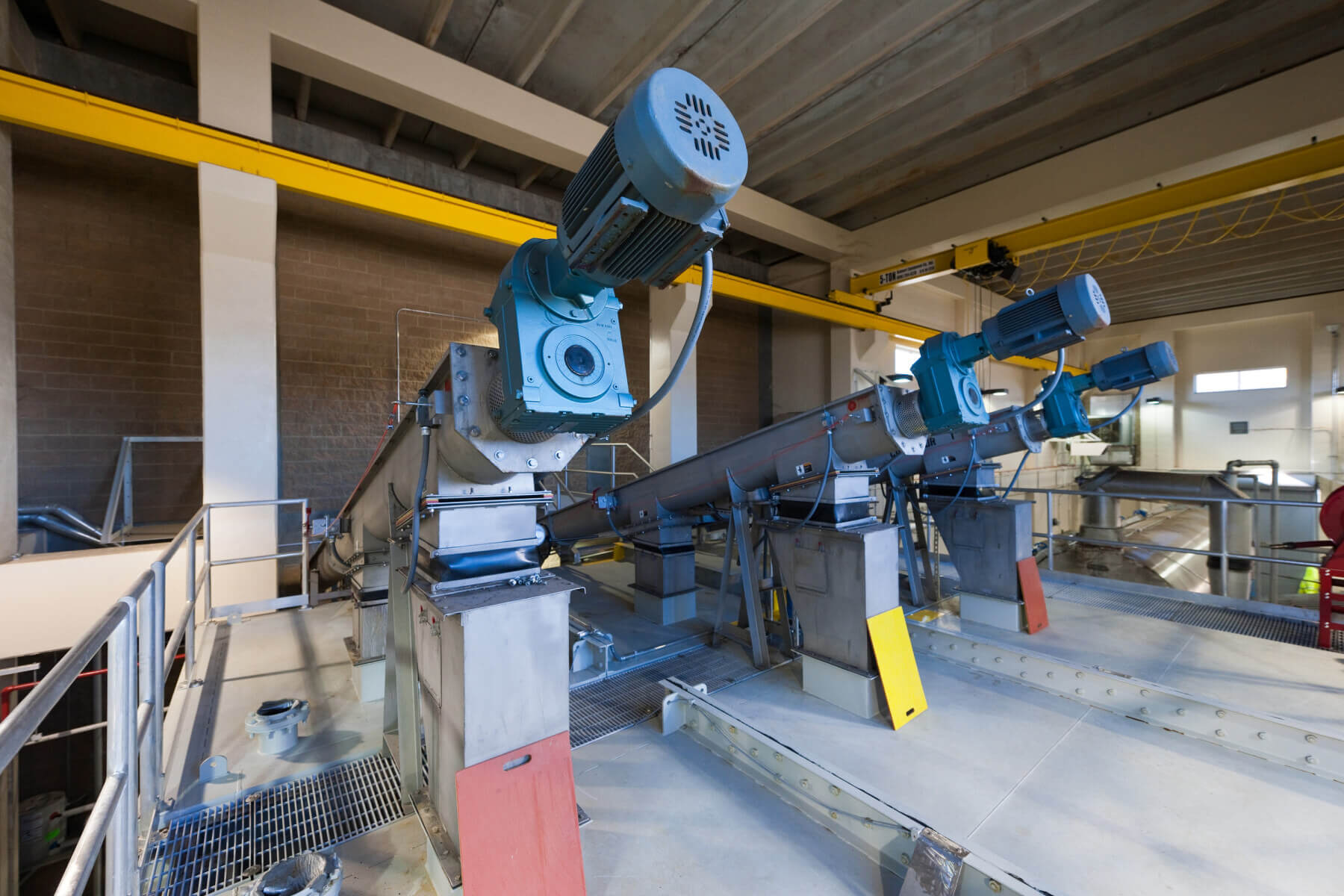
In addition to the new sequencing batch reactor and thermal dryer, the renovated plant includes a new headworks and influent pump station, improved odor control mechanisms, a septage receiving station, high-efficiency turbo-compressor blowers, ultraviolet disinfection equipment and dewatering centrifuges. Updated instrumentation and controls allow operators overseeing the process to monitor and control operations with real-time data response technology.
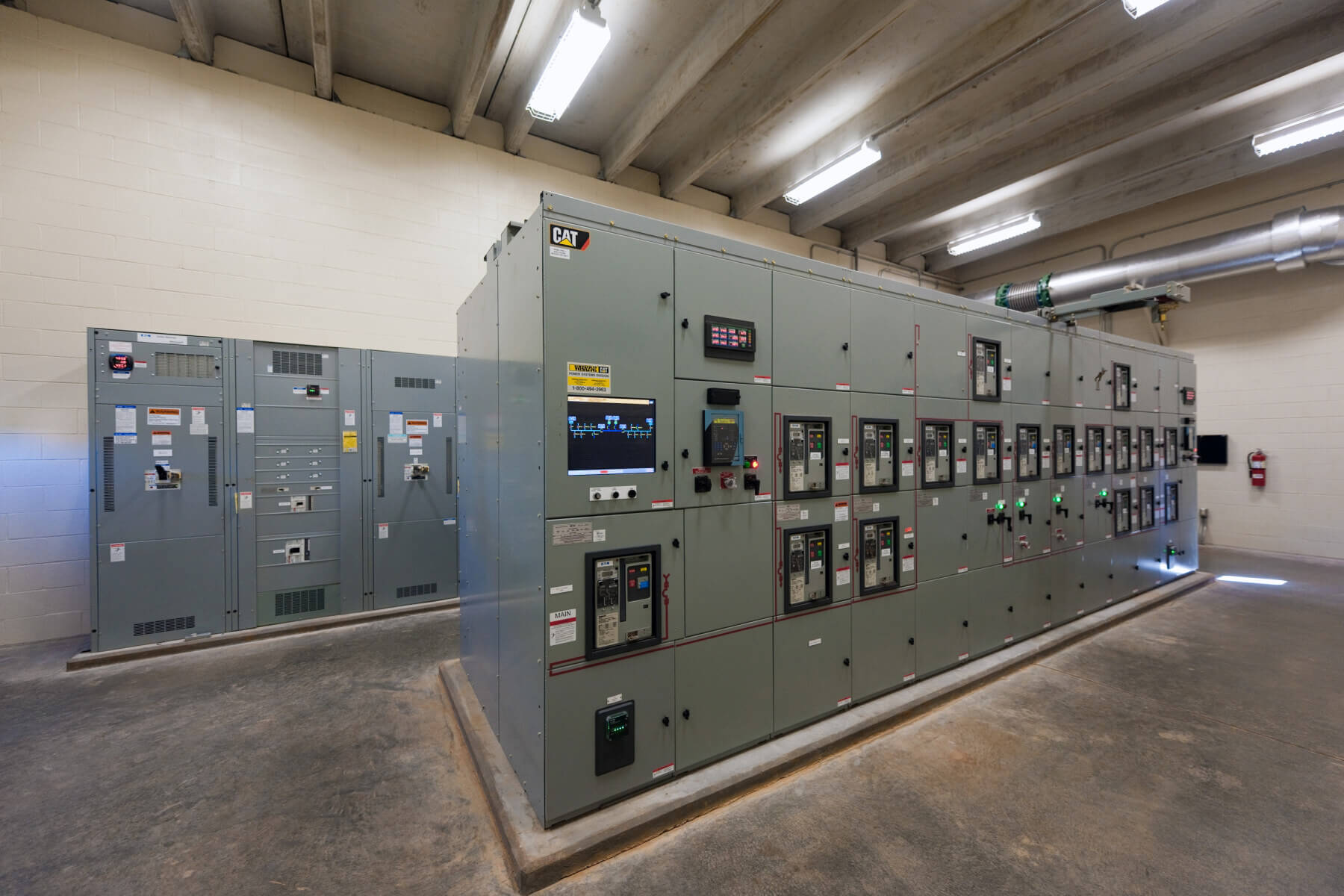
Gresham Smith is also designing a replacement to the existing odor control system with a two-stage solution: a bioscrubber, which will use biological processes to degrade the problematic gases, and a carbon absorber, which will absorb any remaining pollutants. The capacity of the headworks building’s ventilation system will be increased to conduct a minimum of 12 air changes per hour and add a supplemental fan to increase total ventilation. Combined, these solutions will treat the air before it’s discharged into the atmosphere.